1概述
汽輪機葉片是一種典型的具有複雜曲麵(miàn)的零件。葉片一般都處在高溫、高壓、高轉速和腐蝕(shí)介質環境下工作,不僅需要有(yǒu)較高的強度,而且要具有較(jiào)高的抗(kàng)腐蝕、抗疲勞、抗衝擊能力。隨著材料科學、設計技術、加工設備的變化和進步,其型麵形狀日趨複雜,其加工工藝也不斷地發生變化(huà)並日臻完善。其(qí)加工要求嚴格,加工(gōng)量很大。
汽輪機(jī)葉片的型麵已經從等截(jié)麵直葉片向變截麵扭葉片發展,其加工工藝也隨之變得愈加複雜,葉片(piàn)型(xíng)麵的造型(xíng)及加工直(zhí)接影響到汽輪機的工作性能。目前,汽輪機葉片一般均采用五坐標聯動數控機床來加工完(wán)成(chéng) 。加工之前(qián)的數控編程是保證葉片加工精度和表麵質量的關鍵。本(běn)文針對(duì)汽輪機(jī)葉片型(xíng)麵的複雜性,先將實測數據經Matlab軟件平滑處理後,導入UG利用NURBS方法對其進行了精確的三維造(zào)型,並進行了葉片的數控加工工藝流程規劃(huá);UG的加工製造模塊(kuài)功能極(jí)強,研究在(zài)同一個CAD、CAM環境下,實現汽(qì)輪機(jī)葉片的三維造型、圖形化數(shù)控編程、刀具軌跡生成、實時加工仿真的方法,以保證數控加工的(de)質量和效率。
2汽輪機葉片的CAD/CAM係統結構圖
UG是一個高(gāo)度集(jí)成的(de)CAD/CAE/CAM軟件係統(tǒng),它不僅具有強大的實體造型、曲麵造型等設計功能,而且可(kě)以(yǐ)運用建立好的三(sān)維模型直接生成數(shù)控代碼,用於產品的加工(gōng)。汽輪機葉片CAD/CAM係統結構圖見圖1。
3創建葉片(piàn)三維模(mó)型(xíng)
3.1葉片數據的獲取方(fāng)法
汽輪機葉片數據的獲取主要有兩種方法:一種是(shì)通(tōng)過逆向工程;一種是通過理論計算。逆向工程(chéng)是把原型的幾何尺寸通過各種測量方法(如:三坐標(biāo)測(cè)量機、激光跟蹤儀、三坐(zuò)標(biāo)測頭等)轉化成數(shù)據文件,然後(hòu)重新建立(lì)此零件的CAD模型的技術。理論(lùn)計算是根(gēn)據(jù)流體力(lì)學原理計(jì)算出的(de)葉型數據。
數(shù)據文件(jiàn)提供(gòng)的是一係列數據點坐(zuò)標,數(shù)據點坐標格式為:“X空格Y空格Z空格”,與UG對數(shù)據源文件(jiàn)的要求一致。這樣才(cái)可以根據曲麵的連續(xù)、光滑性要求,在UG的自由曲麵模塊中,由葉(yè)片(piàn)的離散數(shù)據(jù)點擬合(hé)生成光(guāng)滑、準確的閉合曲(qǔ)線,從而再通過這些曲線生成葉片曲麵。
3.2葉(yè)片數(shù)據的平滑(huá)處理
本(běn)文以某(mǒu)汽輪機葉(yè)片製造企業提供的一隻汽(qì)輪機靜葉片造(zào)型(xíng)為例。如圖(tú)2所示,該葉片(piàn)某截麵包含有各截麵型線(xiàn)的葉盆、葉背(bèi)型值(zhí)點參數,其中,(X_S,Y_S)為該截麵背弧曲線上的型值點坐標值(zhí),(X_P,Y_P)為盆弧曲線上的(de)型值點坐標(biāo)。無論是盆弧還是背弧均給(gěi)出了51個型值點。
本文數據通過逆向工程獲得,測量時由於人為(wéi)因素或其他因素(測量(liàng)儀器本身的誤差),導致測量值與實際值存在一定的誤(wù)差。對測量值進行平滑處理,目(mù)的就是使得測量值與實際值之間的誤差減小。在多軸加工中,曲麵的光順性及(jí)曲麵間的(de)光滑連接特性對生(shēng)成多軸數控加工程序的質量影(yǐng)響很大,這就對葉片型(xíng)麵的幾何建模(mó)提出了更高的(de)要求。葉片型麵的高(gāo)質量幾何建模,首(shǒu)先是指型麵在各截麵型線方向上要保持光順。其次,在葉片徑向上曲麵也要求同樣保持(chí)光順。將(jiāng)圖2中測量值導入Matlab軟件,通過CFTOOL工具和Smooth函數(shù)對測量值進行平(píng)滑處理。處理後數據如圖3所示(shì)。通過對葉片截(jié)麵型線型值點進行平滑處理,使得葉片截麵型線比處理前更平滑(huá)更接近葉片實(shí)際截麵型線。將處理後的數據輸出(chū)並保存為.dat文(wén)件。為下一(yī)步UG建立汽輪機葉片三(sān)維模型做準備。
3.3汽(qì)輪機(jī)葉片三維實體造(zào)型
汽輪機葉片一般由葉根、葉(yè)身(shēn)和葉冠三部分構成。葉根(gēn)和葉冠的形狀相對規則,可以直接通過草繪截麵,拉伸為實體。再在實體造型的基礎上進行打孔、開槽、倒圓、倒角(jiǎo)等操作即可得到實體模型。而葉身部分是汽流通(tōng)道,形狀比較複雜。葉身的橫截麵稱為型麵,組成(chéng)型麵的周(zhōu)線稱為型線。葉(yè)片的葉身就是由這些型線擬合而成的光滑複雜曲麵。
圖3 平滑處理(lǐ)後(hòu)的數據(jù)
(1)數據導入
將Matlab軟件平滑處理後的數據(jù).dat文件導入 UG中。導入方法:點擊UG中的樣條曲線按鈕,出現根據極點、通(tōng)過點、擬合、垂直於平麵(miàn)4個(gè)提示選項。選擇“通過點”,然後點擊(jī)選項“文件中的點”,選取數據.dat文件即可建立樣條曲線。
(2)草圖編輯
對建立的樣條曲線進行草圖(tú)編(biān)輯。圖(tú)4為草圖編輯(jí)後葉片截麵型線。
(3)曲線分析
用UG中的(de)曲線分析工具,分析葉片截麵型線的曲率分布情況,有無斷點、尖點、交叉、重疊。下麵以一條型線為例,分析曲線的(de)質量。曲率梳(shū)可以(yǐ)反映曲線的曲率變化規律並由此發現(xiàn)曲線的形狀存在的問題。通過編輯(jí)曲線中的光(guāng)順曲線命令,修改光順因子,來達到需要的光順曲線。光順後的曲線(xiàn)更有(yǒu)利於後續的數控加(jiā)工編程。圖5為葉片截麵型線背弧段的光順處理。
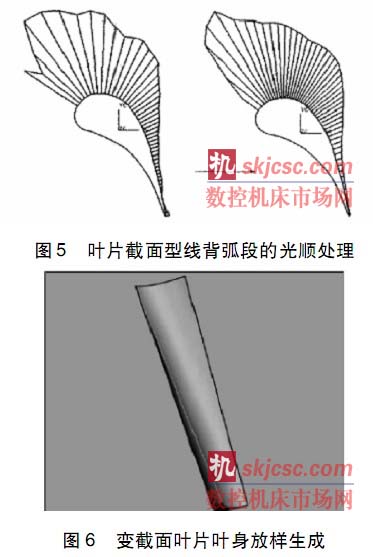
(4)葉身生成
葉片葉身采用多(duō)截麵導動(dòng)的方法來生成,如圖6所示。
4汽輪機葉片數控加工自動編程
(1)葉片的加工工(gōng)藝分析
葉片的毛坯一般是鑄造或(huò)精鍛而成,留出一定的加工(gōng)餘量。當葉片尺寸比(bǐ)較小的時候也(yě)可以直接用(yòng)方坯(pī)料開始加工。葉型曲麵的加工常用沿(yán)著葉片
軸線加工和沿截麵型線加工兩種加工方案。由於沿葉片軸線加工出來的汽道表麵質量較差,本文采(cǎi)用沿(yán)截(jié)麵型線加工的方法。
由於葉型(xíng)是光滑連續的曲麵,所以用一刀(dāo)成形的方法,生成沿型線連續的刀具軌跡,並一次(cì)加工(gōng)完(wán)成。
用五軸(zhóu)聯動數控機床加工葉型曲麵的主要工藝過程(chéng)為 :①粗加工:這個過程的主要目的是去(qù)除多餘的毛坯料,加工出葉型曲麵的大(dà)體輪廓。②半精加工:這個過程要加工出葉型曲麵的基本形狀,並留出少量的加工餘量,為精加工做準備。③精加工(gōng): 這個過程要加工出葉型的(de)整個型麵,過程和半精加工類似,但需要取較小的行距和(hé)表麵允差,以提高表麵的加工質量(liàng)。
(2)UG/CAM基本設置
首先確認工作坐標係原點然後進入加工(gōng)模塊(kuài)進行相關設置:設置安全(quán)高度(dù);設置幾何體包括指定部件和指定毛坯;設置加工公差;創建刀具。
刀具選擇。加工葉片的整個過程要用到3種刀:端銑刀(dāo)(粗加工用(yòng))、球頭銑刀(半精加工(gōng)和精加工用(yòng))和(hé)球頭錐銑刀(清根用)。
加工方式的(de)選擇。在UG/CAM中為每個(gè)工序選擇(zé)合適(shì)的加工方式,其中半精加工和精加工的加工(gōng)方式相同。
刀具軌跡的生成。在UG/CAM中,選擇合適的加工方式、加工對象和走刀方式等(děng)後(hòu),再設置好切削(xuē)行(háng)距、步長、表麵允差、進給率等加工參數,即可以執行(háng)[Genemte]命令生成刀具加工軌跡。
加工過程仿真。UG/CAM中集成了加工仿真的(de)功能,可以對生(shēng)成的刀具軌跡進行加工(gōng)仿真,動(dòng)態的模擬刀具切除材料的(de)加工過程,並且可(kě)以儲存加工(gōng)仿真後的毛坯留待下一(yī)道工序使用(yòng)。在UG環境下,通過加工仿真對刀具軌跡(jì)進(jìn)行仿真和驗證。
刀位文件(jiàn)生成及後置處理。在UG/CAM中生成了刀具軌跡並進行了加工仿真和幹涉校驗後,可以將加工數據和信息輸出成為刀位(wèi)源文件(CLSF)。刀位源文件(CLSFF)主(zhǔ)要包括刀具(jù)信息、加工坐標係信息、刀具位(wèi)置和姿態信息以及(jí)各種加工輔助命令信息等。單擊“操作”中(zhōng)的“後置處理”可以生成葉片加工的NC代碼(mǎ)。
5結語
在UG環境下,結合Matlab軟件強大的數據處(chù)理功能,對葉片的精確造型進行分析。在UG中進行葉片的三維造型,進行加工、刀(dāo)具(jù)軌跡編程和加工仿真,使汽輪機葉片的設計和(hé)加工編程基於同一(yī)個CAD/CAM環境下。這(zhè)就實現了產品設計和製造過程信息模型的無縫連接,大大減小(xiǎo)了編程出錯概率,提高了編(biān)程效率和可靠性(xìng)。
如果(guǒ)您有機床行業、企業相(xiàng)關新聞稿件發表,或進行資訊合作,歡迎聯係本網編輯部, 郵箱:skjcsc@vip.sina.com