模具高速加工技術與策略
2013-3-25 來源: 作者:
1 引言
作為現代先進製(zhì)造技(jì)術中最重要的共(gòng)性技術之一(yī)的高速加工技術代表了切削加工的發展方向,並逐漸成為切削加工的主流技術。高速切削中(zhōng)的“高速”是一個相對概念(niàn),對於不同的加工方式及工件材料,高速切削(xuē)時采用(yòng)的切削速(sù)度(dù)並不相(xiàng)同。一般來說,高速切削采用的切削速度比常規(guī)切削速(sù)度高5~10倍以上。由於高速切削技術的應用可顯著提高加工效(xiào)率和(hé)加工(gōng)精度、降低切削力、減小切削熱對工件的影響、實現工序集約化等,因此已在航空航天、模具製(zhì)造、汽車製造、精密機械等領域得到廣泛應用,並取得了良好的技術經濟(jì)效益。在現代模具的成形(xíng)製造(zào)中,由於模具的形麵設計日趨複雜,自由曲麵所占比例不斷(duàn)增加,因(yīn)此對模具(jù)加工技術提(tí)出了更高要求,即(jí)不僅應保證高的製造精度和表麵質量,而且要追求加工表麵的美觀。隨著對(duì)高速加工技術的研究不斷深入(rù),尤其在加工機床、數(shù)控係統、刀具係統、CAD/CAM 軟件等相關技術不斷發展的(de)推動下,高速加工技術(shù)已越來(lái)越多地應用於模具的製造加工。
高速加工技術對模具加工工藝產生了(le)巨大影響,改變了(le)傳(chuán)統模具加(jiā)工采用的“退火→銑(xǐ)削加工→熱處理(lǐ)→磨削(xuē)”或“電火花加(jiā)工→手工(gōng)打磨、拋光”等複雜冗(rǒng)長的工藝流程,甚至可用高速切削(xuē)加工替代原來的全部(bù)工序。高速加工技術除(chú)可應用於淬(cuì)硬模具型腔的直接加(jiā)工(尤其是半精加工和精加工)外,在EDM電極加工、快速樣(yàng)件製造等(děng)方麵也得到廣泛應用。大量生產實踐表明,應用高速切削技術(shù)可節省模具後續加工中約80%的手工研磨(mó)時(shí)間,節約加工成本費用近30%,模具表麵加工精度可達(dá)1μm,刀具切(qiē)削效率可提高一倍。
2 模具高速加工對加工係統的要(yào)求
由於(yú)模(mó)具加工的特殊性以及高速加工技術的自身特點,對模(mó)具高速加工的相(xiàng)關(guān)技術及(jí)工藝係統(加工機床、數控係(xì)統(tǒng)、刀具等)提出了比傳(chuán)統模具加工更高的要求。
2.1機床主軸
高速機床(chuáng)的主軸性能是實現高速切削加工的重要條件。高速切削(xuē)機床主軸的(de)轉(zhuǎn)速(sù)範圍為10000~100000r/mim,並要(yào)求主軸具有快速升(shēng)速、在指定位置快速準停的性能(即(jí)具有極(jí)高的角加減速(sù)度),因此高(gāo)速主軸常(cháng)采用液體靜壓軸承式、空氣靜壓軸承式、磁懸浮軸承式等結(jié)構形式。
2.2機床驅動(dòng)係統(tǒng)
為滿足模具高速加(jiā)工的需要,加工機床的驅動係統應具有下列特性(xìng):
高的進給速度。研究表明,對於小直徑刀具,提高轉速(sù)和每齒進給量有利於降(jiàng)低刀具磨損。目前常用的進給速度範圍為20~30m/min,如采用(yòng)大(dà)導程滾珠絲杠傳動,進給速度可達60m/min;采用直線電機則可使進(jìn)給速度達到120m/min。高的加速度。對三維複雜曲麵廓形的高速加工要求驅動係統具有良好(hǎo)的加速度特性,驅動係統加速度應達到20~40m/s2。高的(de)速度增益因子(Velocity gain factor)Kv。為達到較高的三維輪廓動態精度以及最小的滯後,一般要求速(sù)度增益因子Kv=20~30(m/min)/mm。
2.3數控係統
先進的數控係(xì)統(tǒng)是保證模具(jù)複雜曲麵高速加工質量和效率的關鍵因素,模具高速切削加工(gōng)對數控係統(tǒng)的基(jī)本要求為:
高速的數字控(kòng)製回路(lù)(Digital control loop)。包括:32位或64位處理器及1.5Gb以上的硬盤;極短的直線電機(jī)采樣時間(<500μs);速度和加速度的前饋控製(Feed forward control);數字驅動係統的爬行控製(zhì)(Jerk control)。
先進的插補方法(基於NURBS 的樣條插補),以獲得良(liáng)好的表麵質量、精確的尺寸和高的幾何精度。
預處理(Look-ahead)功能。要求具有大(dà)容量緩衝寄存器,可預先閱讀和檢查多個程序段(如DMG 機床(chuáng)可多達500 個程序段,Simens 係統可達1000~2000 個程序段(duàn)),以便在被加工表麵形狀(曲率)發生(shēng)變(biàn)化時(shí)可及時采取改變進給速度等措施以避免過切等。誤差補償功能。包括因直線電機、主軸等發熱導致的熱誤差補償、象限誤差補償、測(cè)量係統誤差補償等功能。此外,模具高速切削加工對數據(jù)傳輸速度的要求也很高。傳統的數據接口如RS232串行口的傳輸速度為19.2Kbps,而許多先進的加工中心均(jun1)已采用以太局域網(wǎng)(Ethernet)進行數據傳輸,速度可達200Kbps。
2.4高速切削刀(dāo)具係(xì)統
高速切削刀具(jù)係統(tǒng)的主要發展趨勢是(shì)空心錐部和主軸端麵同時接觸的雙定位(wèi)式刀柄(如德國OTT公司的HSK刀柄、美國Kenamental公司的KM刀柄等),其軸向定位精度可達0.001mm。在高速旋轉的離心(xīn)力作用下,刀夾鎖緊更為牢固,其徑向跳動不超(chāo)過5μm。用於高速切削加工的(de)刀具材料主要有硬質合金、陶瓷、金屬陶瓷、立方氮化(huà)硼(PCBN)、聚(jù)晶金剛石等(děng)。為滿足模具高速加工的要求,刀具(jù)技術的(de)發展主(zhǔ)要集中在新型塗層(céng)材料與塗層方法的研究、新型刀具結構的開發等方麵。
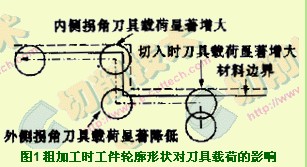
3 模具高速加工工藝及策略
3.1粗加工
模具粗加工的主要目標是追求單位時間(jiān)內的材(cái)料去除率,並(bìng)為半精加工準備工(gōng)件的幾何輪廓。圖(tú)1所示為粗加工過程中工件(jiàn)輪廓(kuò)形狀對(duì)刀具載荷(hé)的(de)影(yǐng)響。由圖可(kě)見,在切削過程中因切削層金屬麵積發(fā)生變化(huà),導致刀具承受的載荷發生變化,使切削過程不穩定,刀(dāo)具磨損(sǔn)速度不均勻,加工(gōng)表麵質量下降。目前開發的許多CAM軟件可通過(guò)以下措施保持切削條件恒定(dìng),從而獲得良好的加工(gōng)質量。恒定的切削載(zǎi)荷。通過計算獲得恒定的切削層麵積和材(cái)料去除率,使切削(xuē)載荷與刀具磨損速率保持均衡,以提高刀(dāo)具壽命和加工質(zhì)量。避免突然改變(biàn)刀具進給(gěi)方向(xiàng)。避免將刀具埋入(rù)工件。如(rú)加工模具型腔時(shí),應避免刀具垂(chuí)直插入工件,而應采(cǎi)用(yòng)傾(qīng)斜下刀方式(常用傾斜角為(wéi)20°~30°),最好采用螺旋式下刀以降低刀具載荷;加工模具型(xíng)芯時,應盡量先從工件外部下刀然後水平切入工件。刀具切入、切(qiē)出工(gōng)件時應盡(jìn)可能采用傾斜式(或圓(yuán)弧式)切(qiē)入、切出,避免垂直切入、切出。采用攀爬式切削(Climb cutting)可降低切削熱,減小刀具受力和加工硬化程(chéng)度(dù),提高加工質(zhì)量。
3.2半精加(jiā)工
模具半精加工的主要目標是使工件輪廓形狀平整,表麵精加工餘量均勻,這對於工具鋼模具尤為重要,因為它將影響精加工時刀具切削層麵積的變化及刀(dāo)具載荷的變化,從而影響切削過程(chéng)的穩定性及精加工表麵質量。
粗加工是基於體積模型(Volume model),精加工則是基於(yú)麵模型(Surface model)。而以前開(kāi)發的CAD/CAM係統對零件的幾何描述是不連續的,由(yóu)於沒有描述粗加工後、精加工前加工模型的中間信息,故粗加工表麵的剩(shèng)餘加工餘量分布及最大剩餘加工餘量均是未知的。因此應對半精加工策略進行優化以保(bǎo)證半精加工後工件(jiàn)表麵具有均勻的剩餘加工餘量。優化過程包括:粗加工後輪廓的計算、最大剩餘加工餘量的計算、最大允(yǔn)許加工餘量的確定、對剩餘(yú)加工餘量大於最大允許加工餘量的型麵分區(如凹槽(cáo)、拐角等過渡半徑小於粗加工刀具半徑的區域)以及半精加工時刀心軌跡的計算等。
現有的模(mó)具高速加工CAD/CAM軟件大都具備剩餘加工(gōng)餘量分析功能,並能(néng)根據剩餘加工(gōng)餘量的大小及分布情況采用合理的半精加工策略。如Open Mind公(gōng)司的Hyper Mill和Hyper Form軟件提供了束狀銑削(Pencil milling)和剩餘銑削(Rest milling)等方法來清(qīng)除粗加工(gōng)後剩餘加工餘量較大的角落以保證後續工(gōng)序均勻的加(jiā)工餘量。Pro/Engineer軟件的局部銑削(Local milling)具有(yǒu)相似的功能,如局部銑削工序的剩餘加工餘量取值與粗加工相等,該工序隻用一把小直徑銑刀來清除粗加工未(wèi)切到的角落,然後再進行半精加工;如果取局部銑削工序的剩餘加工餘量值作為半精加工的剩餘加工餘(yú)量,則該工序不僅可清(qīng)除粗加工未切到的角落,還可完成半精加工(gōng)。
3.3精加工
模具的高速精(jīng)加工策略取決於刀(dāo)具與工件的接觸點,而刀具與工件的接觸點隨著(zhe)加工表麵的曲麵(miàn)斜率和刀(dāo)具有效半徑的變化而變化。對於(yú)由多個曲麵組合而成(chéng)的複(fù)雜曲麵加工(見圖2),應盡可能在一個工序中進行連續加工,而不是對各個曲麵分別進行加工,以減少抬刀、下刀的次數。然而由於加工中表麵斜率的變化,如果隻定義(yì)加(jiā)工的側吃刀量(Step over),就可能造成在斜(xié)率不同的表(biǎo)麵上實際步距不均勻,從而影響加(jiā)工(gōng)質量。
Pro/Engineer解決(jué)上述問題的方法是在(zài)定義側吃刀(dāo)量的(de)同時,再定義加工表麵殘留麵積高度(Scallopheight);Hyper Mill 則提供了等步距加工(Equidistantmachining)方式,可(kě)保證走刀路徑間均勻的側吃刀量(liàng),而不受表(biǎo)麵斜率及曲率的限製,保證刀具在切(qiē)削過程中始終承受均勻的載荷。一般(bān)情況下,精加工(gōng)曲麵的曲率半徑應大於刀具半(bàn)徑的1.5倍,以避免進給方向的突然轉變。在模具的高速精加工中,在每(měi)次切入、切出工件時,進給方向的改(gǎi)變應盡量采用圓弧或曲(qǔ)線轉接,避免采用直線轉接,以保持切削過程的(de)平穩性。
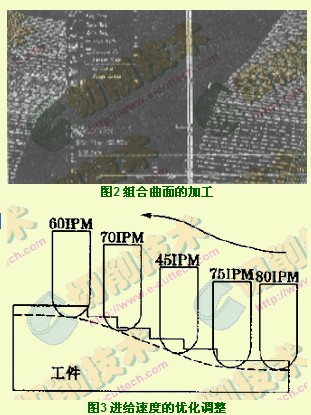
3.4進給速(sù)度的優(yōu)化
目前(qián)很多(duō)CAM軟(ruǎn)件(jiàn)都具(jù)有進給速度的優化調(diào)整功能(如圖3所示):在(zài)半精加工過程中,當(dāng)切削層(céng)麵積大時降低進給速度,而切削層麵積小時增大進給速度。應用進給速度的優(yōu)化調整可使切(qiē)削過程平穩,提高(gāo)加工表麵質量。切削層(céng)麵積的大小完全由CAM軟件自動計算,進給速度的調整可由用戶(hù)根據加工要求來設置。
投稿箱:
如果您有機床行業、企業相關新(xīn)聞稿件發(fā)表,或進行資訊合作,歡迎聯係本網(wǎng)編輯部, 郵箱:skjcsc@vip.sina.com
如果您有機床行業、企業相關新(xīn)聞稿件發(fā)表,或進行資訊合作,歡迎聯係本網(wǎng)編輯部, 郵箱:skjcsc@vip.sina.com
更多本專題(tí)新聞
專題(tí)點擊前十
| 更(gèng)多